Power transformers can be classified in various ways, but the most common types are oil-immersed transformers, dry-type transformers, and compact substations. Today, we’ll focus on dry-type transformers.
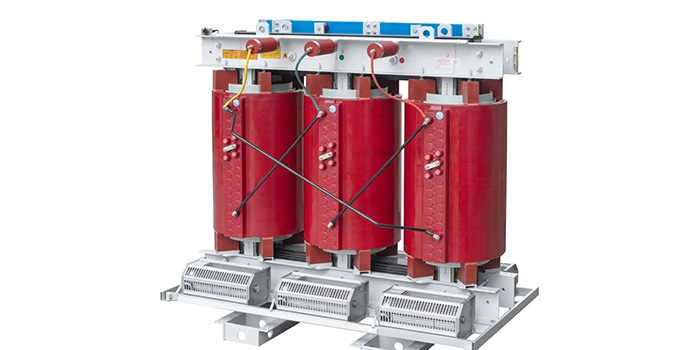
Cooling and Insulation of Dry-Type Transformers
A dry-type transformer is a special type of power transformer where the core and windings are not immersed in insulating oil.
This raises a question: oil-immersed transformers rely on insulating oil for cooling and insulation, so how do dry-type transformers achieve this without oil?
First, let’s discuss cooling. Dry-type transformers typically use two cooling methods:
- Natural Air Cooling (AN): Under rated capacity, the transformer relies on natural air convection for heat dissipation, allowing continuous operation without additional cooling equipment.
- Forced Air Cooling (AF): When the operating temperature reaches 80°C, the temperature control system automatically activates fans to enhance cooling, improving heat dissipation efficiency and enabling stable operation under overload or high-temperature conditions.
For insulation, dry-type transformers primarily use epoxy resin as the insulating material, employing various techniques such as:
- Vacuum casting with epoxy-quartz sand mixtures
- Vacuum differential pressure casting with epoxy-reinforced alkali-free glass fiber
- Alkali-free glass fiber winding impregnation
Advantages of Dry-Type Transformers
- High Safety: No flammable oil means reduced fire or explosion risks, enhancing operational safety. Excellent electrical insulation also prevents leakage and short circuits.
- Eco-Friendly: No oil eliminates pollution risks, making them environmentally friendly.
- Energy-Efficient: Optimized coil design, high-efficiency insulation, and advanced manufacturing reduce energy loss and improve performance.
- High Reliability: Advanced materials and processes ensure long service life and low failure rates, supporting stable power systems.
Disadvantages of Dry-Type Transformers
- Poor Moisture/Dust Resistance: Vulnerable to humidity and dust, often requiring protective enclosures or dedicated rooms.
- Limited Outdoor Suitability: Best for indoor use; outdoor installations need extra protection and cooling measures.
- High Insulation Material Requirements: Specialized materials (e.g., epoxy resin) increase manufacturing costs.
- Difficult Repairs: Damaged coils usually require full replacement, raising maintenance complexity and costs.
Differences from Oil-Immersed Transformers
- Appearance: Oil-immersed transformers have metal casings, while dry-type transformers expose the core and windings.
- Cooling/Insulation: Oil-immersed types use oil; dry types rely on air.
- Structure: Dry-type transformers are lighter and more compact due to no oil. Windings and cores are wrapped in multi-layer insulation and protective coatings. The laminated iron core minimizes magnetic loss.
- Applications: Dry types excel in indoor, fire/explosion-prone areas (e.g., buildings). Oil-immersed types dominate outdoor, high-capacity settings like power grids and substations due to superior heat dissipation and load tolerance.
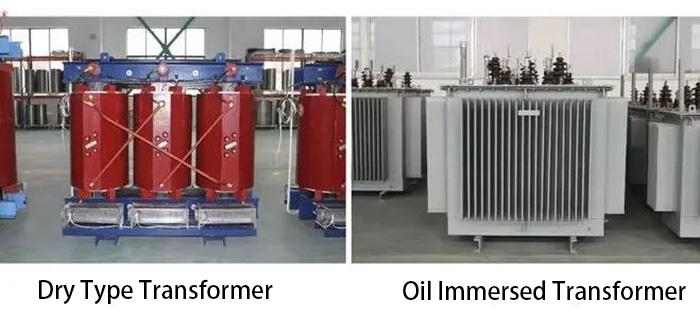