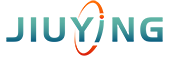
What Are You Looking For?
In regions plagued by persistent humidity, the phenomenon of condensation becomes a critical concern. While the primary circuit of a ring main unit (RMU) is safeguarded within a hermetically sealed gas-insulated tank—impervious to atmospheric moisture—its secondary circuits and mechanical operating mechanisms remain vulnerable. These components demand robust protective measures against moisture ingress. A particularly overlooked hotspot is the fuse compartment, where condensation can be both insidious and destructive.
A case in point: An industrial installation in coastal Australia utilized an RMU housed within an outdoor cabinet. The system was routinely energized at dawn and shut down at night under no load. During a routine fuse replacement, technicians discovered severe corrosion on the fuse holder. The fuse chamber met IP67 ingress protection standards and was meticulously sealed with silicone rubber to ensure dielectric withstand between the high-voltage fuse and cabinet walls. No external moisture intrusion was possible, rendering the corrosion a perplexing anomaly.
Given the coastal proximity of the installation and the user-supplied fuse component, environmental conditions during installation become key variables. The fuse installation occurred in midsummer—a period marked by high ambient humidity. Assuming an installation environment of 20°C and 80% relative humidity, the dew point temperature was approximately 16.4°C. Once the fuse was installed and the chamber sealed, the internal environment was effectively isolated.
Now, consider a slightly different scenario with ambient conditions at 25°C and 60% relative humidity. This yields a dew point of 16.7°C. When the equipment shuts down overnight, ambient temperatures may plummet to as low as 5–10°C. The colder external air cools the fuse chamber through conduction, causing interior surfaces—especially the metallic fuse cap and catch—to dip below the dew point. This microclimatic disparity leads to cyclic condensation inside the chamber, oxidizing silver plating and progressively corroding the fuse holder.
To mitigate such degradation, RMU designs must adapt for humid deployment zones. Ensuring dryness within the high-voltage fuse compartment is paramount. During fuse replacement, ambient humidity should be carefully controlled, and exposure minimized. In critical applications, substituting the traditional RMU configuration with a circuit breaker panel might be necessary to eliminate this vulnerability entirely.
Altitude exerts a profound influence on the performance and integrity of gas-insulated RMUs. Though the gas-tight sealed chambers shield the live components from external dielectric stress, altitude primarily affects the mechanical pressure differential across the chamber walls.
Consider an installation in the Andean highlands of South America, where altitudes commonly reach 3,500 meters above sea level. At this elevation, atmospheric pressure drops to approximately 0.065 MPa. If the RMU's internal gas pressure is 0.13 MPa (absolute), the resulting pressure differential with the ambient environment becomes significant—0.065 MPa. Compare this with a mere 0.04 MPa at 1,000 meters elevation, and the escalation becomes evident.
Such pressure gradients can cause the gas tank to swell, and in extreme cases, rupture—triggering gas leaks and compromising insulation. To counteract this, reinforced gas enclosures are essential. Structural enhancements to pressure relief valves and sealing gaskets must be incorporated. Additionally, reducing the internal pressure—without sacrificing dielectric integrity—can help balance internal and external forces.
Transport logistics must also factor into the design. If units are to be shipped through high-altitude regions, temporary depressurization or transportation at atmospheric pressure ensures that tanks remain uncompromised during transit. Maintaining gas tightness and structural integrity through all stages—from factory to field—is non-negotiable.
In the arid, sun-scorched deserts of the Middle East, photovoltaic power stations often rely on 36kV RMUs housed in outdoor enclosures. These cabinets, commonly rated at IP43, offer insufficient protection against pervasive sand and dust particles. Coupled with ambient temperatures soaring above 50°C, the internal temperature of these enclosures can reach alarming levels.
Such conditions conspire to degrade RMU performance. Switch mechanisms stuck in the closed position have been traced to several co-occurring factors: the intrusion of fine dust into the mechanical linkages, the evaporation or carbonization of lubricants under extreme heat, and the accumulation of abrasive residues along semi-axial components. Additionally, polymeric materials within the actuator assembly can soften, deform, or lose tensile strength at prolonged elevated temperatures. The net result? Switchgear that refuses to open when commanded.
To preempt such failures, high-temperature testing must be integrated into the qualification process. A recommended protocol includes placing the RMU inside a thermal chamber at 70°C, with the switchgear in the closed position for 24 hours. Following thermal soaking, the device undergoes electrical opening and closing cycles, with control voltage and actuation velocity meticulously logged. This regimen evaluates the resilience of mechanical and electrical subsystems under extreme thermal stress and ensures functional reliability.
Ring main units, though robust by design, demand nuanced engineering foresight when deployed in atypical environments. From the silent creep of condensation in humid climates, to the strain of atmospheric rarefaction at altitude, and the abrasive fury of desert sands—each environmental vector calls for tailored countermeasures. RMUs that perform flawlessly in standard conditions may falter when exposed to nature's extremes. Only through vigilant adaptation in design, testing, and operational protocols can their reliability be truly guaranteed across the globe’s most unforgiving terrains.